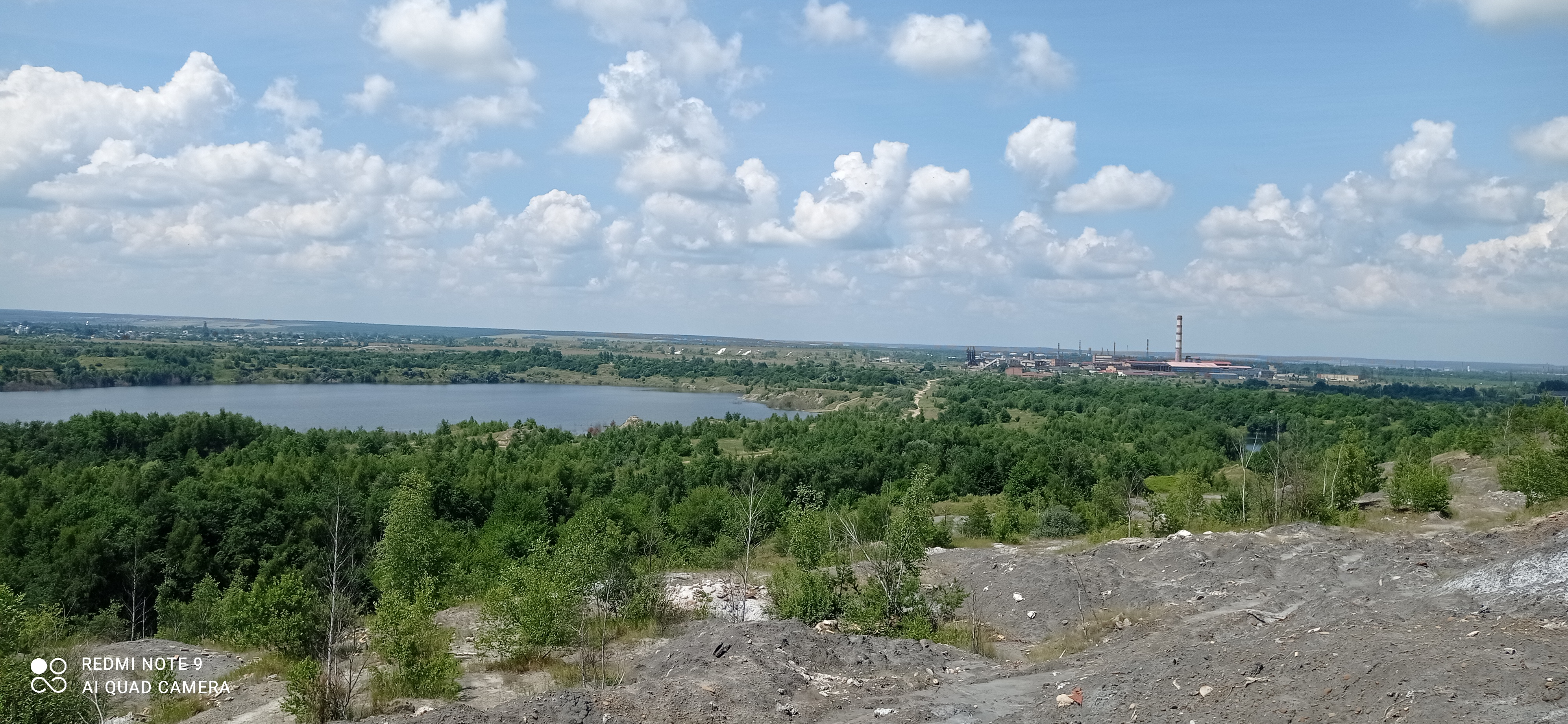
Фіртка продовжує цикл публікацій про Домбровський кар’єр, що нині є екологічною бомбою уповільненої дії, проте може перетворитись на рентабельний проєкт.
Для уникнення екологічної катастрофи в районі Калуського соляного родовища необхідно переробити великі об’єми розсолів із різною концентрацією.
Постає вкрай важливе запитання: а чи є економічно ефективною технологія перероблення розсолів, і скільки державі коштуватиме повністю переробити розсоли за неефективною технологією.
У численних інтерв’ю, на форумах та конференціях вчені та експерти часто виносять на загал думку про необхідність виділення державних коштів у значних розмірах для перероблення розсолів Домбровського кар’єру.
Також останнім часом висловлюється думка, що держава краще б витрачала кошти, які за весь час виділені на Домбровський кар’єр та на неуспішні спроби утилізувати гексахлорбензол, саме на перероблення розсолів Домбровського кар’єру, то загрозу б ліквідували.
Проаналізувавши ці висловлювання, можна дійти висновку, що наявні технології перероблення розсолів є збитковими та потребують при їх використанні додаткових дотацій з бюджету саме на відшкодування збитків, що виникають в процесі перероблення всього об’єму розсолів, у розмірі близько 200 млн доларів.
Спеціалісти, які вивчали питання, твердять, що перероблення розсолів із концентраціями понад 350 г/л має свій додатній економічний баланс, а при зниженні концентрації хоча б на 50 г/л, - економіка виробничого процесу різко погіршується.
Без збитків і з користю
Водночас спеціалісти ТОВ «Оріана Еко» та науковці Харківського інституту проблем машинобудування зазначають, що перероблення не є збитковим, і його можна вивести на прибутковий рівень.
В чому відмінність точок зору на перероблення? У відмінності технологій.
Якщо дослідити склад солей у розсолі Домбровського кар’єру і задатись ціллю здійснити перероблення, то теоретично із цього розсолу можна добути:
- мінеральні добрива - калій магнезію (найчистіший продукт) – близько 23-28 %;
- чисту технічну сіль - хлорид натрію (відповідає найвищим технічним вимогам будь-якого виробництва) – близько 65-70%;
- бішофіти (найвищої якості) – близько 3-5%;
- залізний сурик (найчистіший фарбник для промисловості) – близько 0,3-0,7%.
В той самий час, всі наявні технології перероблення, які розроблені донедавна, дозволяли здійснювати перероблення, при якому не повністю розділялись добуті речовини, і їх склад виглядав наступним чином:
- мінеральні добрива калію магнезію – близько 7-12%;
- технічна сіль – близько 30-45%;
- нерозділена соляна суміш 30-60%.
Відсоток видобутих речовин у співвідношенні до нерозділених соляних сумішей варіювався в залежності від тієї чи іншої наявної технології, яку застосовували в лабораторних умовах при дослідженні виробничих процесів.
І найефективнішою на певний момент виглядала технологія, при застосуванні якої суміш нерозподілених солей знижувалася максимально до 30% від всієї виготовленої продукції.
Друга проблема цих технологій полягала в тому, що застосування їх не передбачало виділення із розчинів зайвих металевих домішок, в першу чергу – заліза та міді, що в кінцевому результаті впливає суттєво на якість виготовленої продукції. Адже, наявність високого вмісту заліза в технічній солі натрій-хлорид та калій магнезії суттєво знижує якість продукції та відповідно – сферу застосування у господарстві, а також різко звужує коло потенційних покупців.
Так, наприклад для потреб ТОВ «Карпатнафтохім» така сіль уже не підійде, оскільки у зв’язку із використанням у їхньому виробництві ліній з німецькими технологіями – просто протипоказано застосування солей із вмістом заліза та іншими домішками. А застосування у сільському господарстві добрив із вмістом домішок можливе лише при вирощуванні окремих, не вибагливих культур (наприклад, для потреб сільського господарства при вирощуванні технічних культур).
Особливості технології
При виведені на ринок України продукції такої якості, зрозуміло, що її збут виглядає проблематичним, оскільки на ринку достатньо конкурентоспроможного продукту цієї групи із показниками найвищої якості при розумній ціні.
Тоді при застосуванні такої технології для перероблення розсолів, легко передбачити, яким буде економічний ефект. З одного боку всі технології перероблення вимагають розігрівів розсолів до великих температур і постійного підтримання цих температур на високих рівнях. Зрозуміло, що таке виробництво є високо енергозатратним. З іншого боку, якби технологія видавала достатню кількість високоякісного продукту, реалізація якого б відшкодовувала всі енергозатрати, то можна було б сказати, що розв'язання проблеми є.
Хибний ефект
В той самий час, наявність при виробництві 30% нерозділених соляних сумішей відразу ж веде рентабельність виробництва на від’ємні значення, оскільки випарювати розсоли із наступними енергозатратами потрібно всі, а виходи продукції – мають 30% відходів, які ще й потрібно окремо утилізувати.
Але, і добута продукція, яка має домішки в першу чергу заліза, – є дуже низької вартості та не затребувана споживачем, через низьку якість. Тоді, в цілому, організація такого виробництва є не тільки збитковою та вимагає постійних дотацій на покриття збитків від діяльності, а й вимагає додаткових затрат на утилізацію і захоронення нерозподілених сумішей.
Якщо ж глянути очима менеджерів по збуту продукції, то вони в один голос скажуть, що захоронення прийдеться робити й всієї добутої продукції низької якості, оскільки збути її – практично не можливо.
Стосовно добутих нерозподілених сумішей солей певний час існувала думка щодо виготовлення з неї протиожеледного засобу, який можна ефективно використовувати в комунальних потребах. Все вірно. Тільки слід все підрахувати. У Домбровському кар’єрі 26 млн м³ розсолів, в яких є солі із різною концентрацією: від 350 г/л (на глибині кар’єру) і 10 г/л (біля поверхні). Приймемо за середнє значення, що концентрація солей по всьому об’єму є 150 г/л. Тоді в процесі виробництва можна добути протиожеледний засіб по всьому об’єму розсолів із концентрацією 50 г/л (30% нерозділених сумішей або – третя частина).
Що ми отримаємо у процесі виробництва? 1 325 000 тонн сухої соляної нерозподіленої суміші, або таки 26 млн м³ такого протиожеледного засобу в розчиненому вигляді. Для порівняння – у велику автоцистерну поміщається рідина об’ємом 30 м³, а отже, при такому виробництві ми отримаємо 883 000 автоцистерн протиожеледного засобу. І це – тільки з розсолів кар’єру.
Оцінивши цей обсяг отриманої продукції, розуміємо, що жодне комунальне господарство такого об’єму протиожеледного засобу не потребує, а відтак – виробництво є не тільки збитковим, а й повністю фінансово недоцільним та таким, що потребує нових додаткових фінансових ресурсів на утилізацію продукції, яка видобута.
Саме з цих причин крім розмов на різних рівнях влади та заяв про те, що ті чи інші посадовці закличуть якихось міфічних інвесторів, до цього часу на практиці до виробництва із залученням колосальних інвестицій справа так і не дійшла. Тому що всі потенційні інвестори, включаючи й сусідів з ТОВ «Карпатнафтохім», застосувавши калькулятор та зробивши не складні підрахунки, описані вище, зрозуміли всю «економічну привабливість» цього проєкту при тих наявних технологіях перероблення.
Акцент на економічну доцільність
З’ясувавши всі ці деталі, група фахівців, які згодом об’єднались у ТОВ «Калуська соляна компанія», а потім увійшли разом з АТ «Оріана» у спільне товариство «Оріана Еко», поставила собі завдання знайти ефективний спосіб перероблення розсолів та розв'язати проблемні питання наявної технології, прибравши усі недоліки.
В цей час група фахівців розробила технологію та провела усі практичні досліди, що підтвердили її дієвість, яка розв’язала описані вище проблеми, і дозволила отримати високоякісну продукцію. Технологічно вирішено в тому числі й наступні недоліки попередніх технологій:
- виділено з розчинів осади заліза та інших домішок,
- розділено всі солі з розчинів у повному об’ємі без нерозділених залишків.
А відтак, застосування цієї технології дозволяє отримати продукцію найвищого ґатунку у наступних пропорціях:
- мінеральні добрива калій магнезію (найчистішого продукту) – близько 23-28 %;
- чисту технічну сіль хлориду натрію без домішок (відповідає найвищим технічним вимогам будь-якого виробництва) – близько 65-70%;
- бішофіти (найвищої якості для застосування) – близько 3-5%;
- залізний сурик (найчистіший фарбник для промисловості) – близько 0,3-0,7%.
Таким чином, нова технологія привела виробничий процес до початкових теоретичних показників і створила повну економічну доцільність її застосування, адже вона дала можливість отримати високоякісну продукцію, при реалізації якої повністю покриваються затрати на їх виробництво та створюється можливість отримання додаткової рентабельності при наявності різних концентрацій вхідного розсолу.
Про що це говорить? Впровадження та застосування цієї технології виводить заздалегідь збитковий і фінансово затратний процес на прибуткову основу: те, що вважалось довгі роки збитковим і фінансово затратним в один момент стає економічно вигідним. А це дає можливість при комплексному застосуванні з іншими заходами швидко ліквідувати усі загрози екологічного лиха в Калуському регіоні без значних фінансових затрат з боку держави.
Андрій Левкович,
депутат Івано-Франківської обласної ради, член комісії обласної ради з питань екології, раціонального природокористування та розвитку туризму, керівник Івано-Франківської торгово-промислової палати
Читайте також:
Домбровський кар’єр: чому неможливо ліквідувати загрозу без повної переробки розсолів?
Домбровський кар’єр. Хто знешкодить екологічну бомбу уповільненої дії?